パシフィックニュース
「誰が作ったとしても、適合のいい義足を提供したい」 技術の均一化と継承のキーとなるダイレクトソケット
義肢
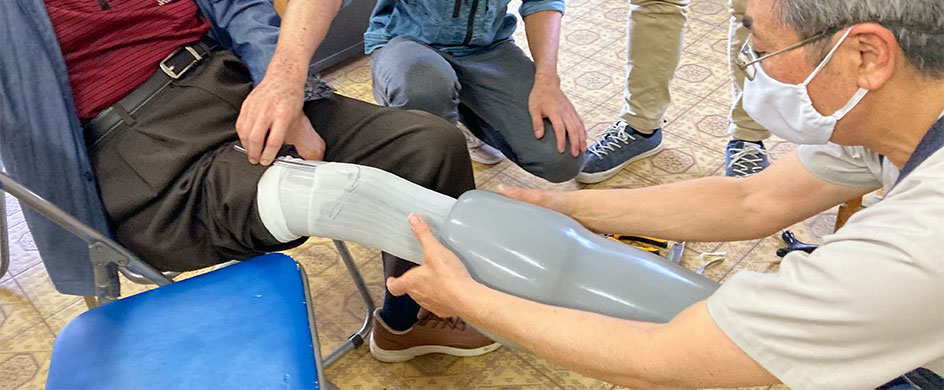
パシフィックサプライ株式会社
事業開発本部 事業推進部 オズール事業推進課
2021-11-15
はじめに
ダイレクトソケットは、切断者の断端上で直接ソケットを採型・製作する技術です。断端の評価から採型、本ソケットの硬化完了までが約1時間で完了します。
従来の石膏による陰性モデルの製作より時間は要しますが、陽性モデルの製作、チェックソケットの製作、本ソケットの樹脂注型などの工程は不要です。
義足製作全体にかかる総製作時間削減の可能性に加えて、チェックソケットによる適合確認工程をなくすことで、切断者の方の来社や来院に伴うご負担を軽減できる可能性があります。
費用面では、従来のチェックソケットを前提とする樹脂注型ソケットが167,700円に対して、ダイレクトソケット(ガラス繊維)は174,500円(カーボン/バサルトの場合:198,000円)となります(内訳は本稿最後に掲載)。
ダイレクトソケットの採型・製作に使用する、専用の加圧採型冶具「ダイレクトソケットツールキット」は改良も進み、より扱いやすいものとなっています。
このダイレクトソケット技術をいち早く採用いただき、これまで4名の方の義足製作に使用された(有)山形義肢研究所の経営者であり、熟練の義肢装具士でもある、植松さまにお話を伺いました。
(有)山形義肢研究所 代表取締役
植松 茂夫さま
ご略歴
昭和30年7月5日生まれ
昭和52年 東海大学卒業
昭和58年 国立障害者リハビリテーションセンター学院 教官
昭和62年 (有)山形義肢研究所 代表取締役 就任
昭和63年 義肢装具士国家資格 取得
(有)山形義肢研究所ホームページ
https://yamagatagishi.com/
植松様とのお話
ダイレクトソケットを採用されたユーザーについて
これまで4名のユーザーにダイレクトソケットを採用しました。年齢は30代、40代、50代、60代の方です。皆さん、本義足の作り替えで、1名は障害者総合支援法にて、他の3名は労災保険の方です。お一人は、ダイレクトソケットのことをご自分でお調べになり、「ぜひこれで義足を作ってほしい」と要望され、製作することとなりました。ユーザーと義肢装具士が共に認める適合品質
ダイレクトソケットで製作したソケットはユーザーの受入れがとてもいいんです。実はダイレクトソケットを採用した4名のなかのお一人は、これまで完成した義足の納品後、何度も適合について修正のご要望に来られる方だったのですが、ダイレクトソケットで製作した義足では、全くそれがないので驚いています。手技の場合でも、骨の突起部は圧が分散するよう丁寧に採型をしていたのですが、専用冶具(ダイレクトソケットツールキット)を使うことで、より全面接触型にフォーカスされたソケットが製作できることが、適合がさらに向上した理由なのだろうと思います。
【動画】Icecastブラダーに圧を加える
【動画】樹脂が硬化後、Icecastブラダーの圧を減らし取り外す
従来のギプス採型と比較して工数が約1/4に
ダイレクトソケットの場合、チェックソケットと陽性モデルの工程が省かれることで、工数が大幅に削減できることは経営的に大きなメリットだと考えています。従来のギプス採型と工数を比較したところ、ダイレクトソケット採型では従来の約1/4でした。
従来のギプス採型とダイレクトソケット採型との製作時間の比較 【山形義肢研究所 植松さまの場合】
(単位:分)
従来のギプス採型 | ダイレクトソケット採型 |
---|---|
340 | 80 |
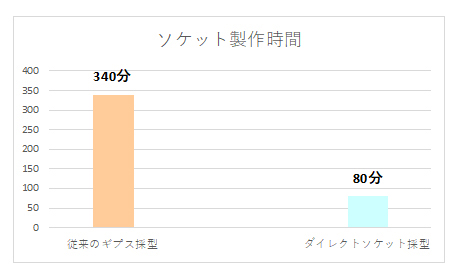
【工程および時間の内訳】
(単位:分)
ギプス採型(陰性モデル) | 30 |
---|---|
【チェックソケット】 | |
陰性モデルにギプスを流す | 20 |
陽性モデル修正 | 40 |
チェックソケット製作 | 60 |
仮合わせ | 60 |
【本ソケット】 | |
チェックソケットにギプスを流す | 20 |
陽性モデル修正 | 20 |
樹脂注型 | 60 |
最終ソケット製作 | 30 |
従来のギプス採型 合計 | 340 |
(単位:分)
パーツ確認・準備 | 10 |
---|---|
断端の確認・Icecast評価 | 10 |
ダイレクトソケット製作(採型用シリコン装着ーブレード装着ーラミネーション) | 15 |
ダイレクトソケットツールキットを装着し硬化 | 10 |
仮合わせ | 15 |
仕上げ | 20 |
ダイレクトソケット採型 合計 | 80 |
ユーザーの満足につながる喜び
採型の日は午前10時頃にユーザーに来社していただき、その日のお時間が許すようであれば、午後に義足をお渡ししています。外装のフォームカバーは後日に仕上げてお渡しということが多いですね。従来の製作方法では、ユーザー側はこれまで3回(採型、仮合わせ、納品時)、仕事を休むなどして時間を捻出していたことは大きな負担だったと思いますが、短期間で義足が完成するので、ユーザーの満足度が非常に高いことがうれしいです。
技術の均一化と継承のキーとなるダイレクトソケット
従来の製造工程と比較し、工数を大幅に減らすことができることはコストダウンにもつながり、経営者として大きなメリットです。私がダイレクトソケットの最も大きいメリットと考えるのは、技術の継承がしやすいことです。これから高齢化が進み、若い義肢装具士に技術を引き継いでいかなければなりません。手技を指導し伝達していますが、手技の場合、個人個人によって結果が若干異なってしまうことは避けられない事実です。しかし、ダイレクトソケットでは、技術の均一化が図れることがとても良いと考えています。加圧値を決めて取り組めば、品質を均等に保つことが可能です。これは我々技術者にとって、そして企業にとって、非常に大きな意味を持っています。
ユーザーにとって、ダイレクトソケットを選択することが100%良いことなのかどうか判断することは難しいですが、80%から90%の満足度は提供できるものと考えています。
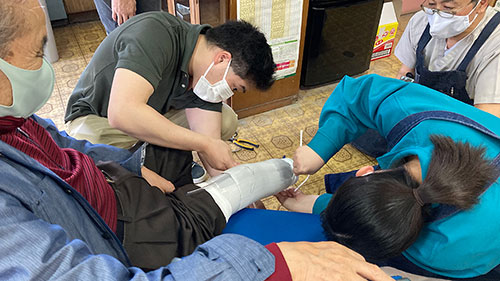
医療の分野(訓練用仮義足)でダイレクトソケットを採用することについて
新規切断の方は、断端のボリュームが変化しやすく、作り直しが発生するリスクがあります。そのため、現在は新規切断の方ではなく、ある程度義足装着歴のあるユーザーに使っていきたいと考えています。その方がユーザーもメリットを感じてもらいやすいんです。製作期間も短く、時間的な負担も少ないうえ、従来のギプス採型では石膏で汚れますが、このダイレクトソケットはきれいに採型できるというメリットもありますしね。
ダイレクトソケット製作の課題
製作時、樹脂が硬化するのが早いので時間との勝負になります。樹脂を流し始めて3~4分が勝負ですので、1名で作業するのは少し大変です。今は2名体制で樹脂を流して作業しています。また、ダイレクトソケットツールキットのコネクタの角度を決めるのが難しいですね。何度も練習を重ねて、慣れていくことが大事だと思っています。また、今のところソケット製作後に修正が必要なケースはありませんが、ダイレクトソケットは完成後に修正ができませんので、採型前に断端をしっかりと評価することが大変重要ですね。
どんな技術でも新しい技術の習得には鍛錬が必要だと思いますので、たくさん練習して自分のものにしていくことですね。
今後への期待
若い人へ技術を引き継いでいきやすいことは大きなメリットと考えていて、他の義肢製作所の方々も関心を寄せられると考えています。講習会や勉強会を通して、義肢装具士がこの技術を実際に見る・体験する機会をたくさん増やしていってほしいですね。「誰が作ったとしても、適合のいい義足を提供したい」
植松さまよりお話を伺い、ユーザーが満足する、適合のいい義足を提供し続けるための技術として、ダイレクトソケットを採用いただいたことが伝わってきました。
ダイレクトソケットは、労働時間の短縮や高齢化による人材不足など、私たちがこれから向き合う社会的な問題に対しても解決の一助となる技術だと確信しています。
集客セミナー、講習会はコロナ禍により難しい状況が続いていますが、オンラインでのセミナーはいつでも開催しております。
「ダイレクトソケットツールキット」に関する情報
サブスクサービス
専用冶具「ダイレクトソケットツールキット」はサブスクサービスとしてもご提供しております。お問合せをお待ちしております。
https://www.p-supply.co.jp/products/index.php?act=detail&pid=772
従来ソケットとダイレクトソケットの費用比較
従来ソケットとダイレクトソケットの費用比較表はこちらからご確認頂けます。https://www.p-supply.co.jp/data/files/00001292-1.pdf (PDF:125KB)
ダイレクトソケットWEBサイト: https://www.p-supply.co.jp/ossur/catalog/icecast-mss/directsocketsystem.html
関連情報
© 2017 Pacific Supply Co.,Ltd.
コンテンツの無断使用・転載を禁じます。
対応ブラウザ : Internet Explorer 10以上 、FireFox,Chrome最新版 、iOS 10以上・Android 4.4以上標準ブラウザ